-
KEMAR >
-
-
-
-
-
-
-
R&D
-
PE
-
PL, QA and QC
-
-
-
-
Got a question?
If you have a question, feel free to contact us:
GRAS Sound & Vibration
Headquarter | gras@grasacoustics.com
UK | sales-uk@grasacoustics.com
USA | sales-usa@grasacoustics.com
China | cnsales@grasacoustics.com
GRAS worldwide
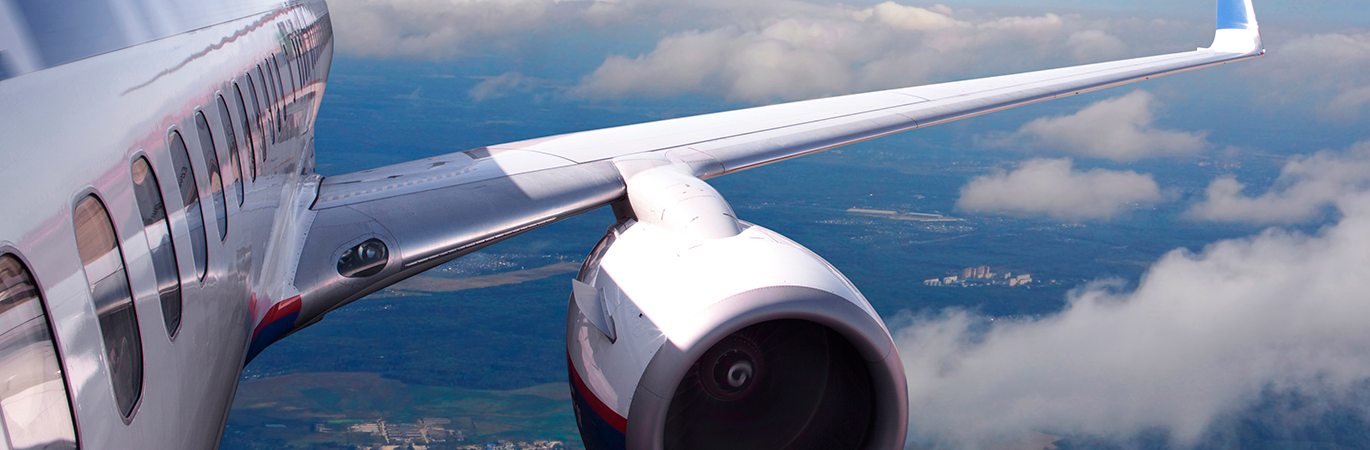
Aerospace and Defense Acoustics
Aeroacoustics is a branch of acoustics that studies noise generation via either turbulent fluid motion or aerodynamic forces interacting with surfaces.
Aeroacoustics is important in the design of aircraft, vehicles, wind turbines, and even buildings and bridges to minimize vibrations and noise.
There are two sources of noise, which are important when talking about aeroacoustics—external noise and aerodynamic noise (or pseudo-noise), see below graphics.
Aeroacoustics is also related to efficiency. Aerodynamics and aeroacoustics are related in that if there is no (or minimal) acoustic noise, there is less turbulence, which is an indication of the aerodynamic efficiency. This relationship is reciprocal.
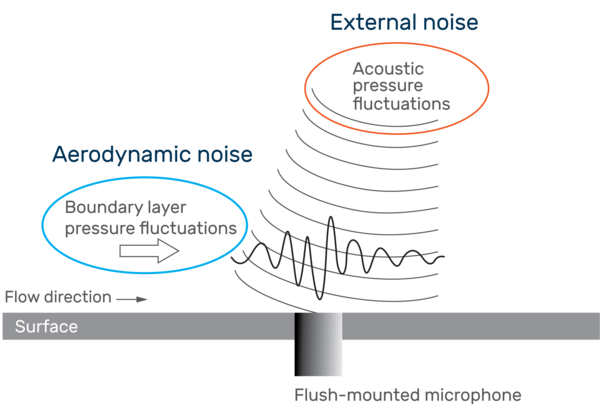
The fundamental problems of aeroacoustics is that most test scenarios are expensive and time-consuming and theoretical tests based on calculation software are difficult to simulate realistically. Due to the complexity of boundary layer pressure variations, simulations often require multiple validations and correctional phases.
Specifically, it is difficult to quantify and understand the turbulence and flow-induced noise on different vehicles (aircraft, cars, and drones), simulation tools are slow and imprecise due to the stochastic behavior of turbulence, experimental acoustic tests are costly due to the need for anechoic wind tunnels, and aircraft generally need to use scale-model aircraft or components that require higher-frequency capabilities.
Aeroacoustics is a critical component in aerospace vehicle design, certification and operation. Typical wind noise sources are shown below.
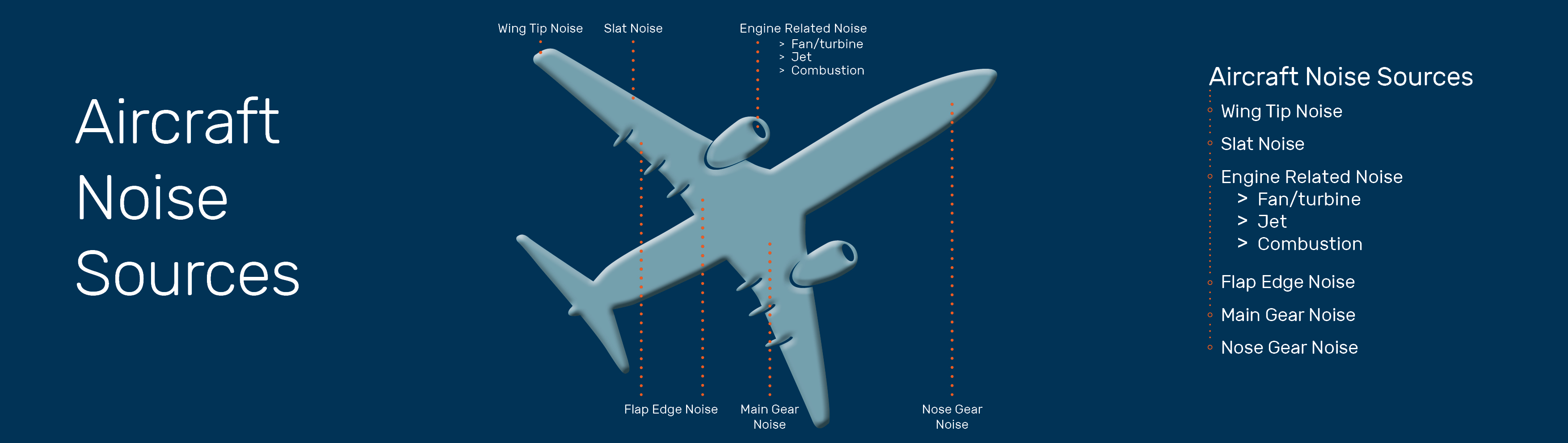
Boundary Layer Measurements
The main focus of wind noise testing in the aerospace industry are measurements in boundary layers. In the aerospace industry, these types of measurements are of increasing importance. The main interest is in separating the acoustic signal from the flow-induced turbulent noise. Purposes span quantifying the amount of sound power radiated from a structure, over sound source localization using an array of microphones to quantifying the turbulent stresses to which a structure is subjected.
Boundary layer theory dictates that measurements must be made exactly on the surface of the structure as the statistics of the flow deviate quickly with increasing distance from the boundary. Moreover, care must be taken not to alter the geometry of the structure as such an action may drastically change the flow. See below illustration.
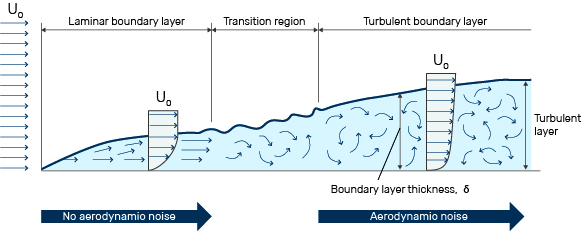
Due to the complexity of measuring boundary layer pressure variations, it is still very difficult to simulate aeroacoustics and often requires multiple validation and correctional phases. Increasing computational power combined with precision microphones from GRAS allow wind tunnel and in flight testing. This helps investigate new aerospace concepts, verify performance of innovative designs through experimental validations of CFD models, and validate prediction models.
There are two methods for mounting microphones for measuring in the boundary layer: Intrusive (flush-mounting) or non-intrusive (surface-mounting).
Flush-mounting is the preferred method because the microphone sits on the same plane as the surrounding surface and does not create additional turbulence.
Explore our range of flush-mount microphones and mounting accessories, such as the 47BG-FV and its reduced-footprint mount.
However, there are times when flush-mounting is not possible, when there is no space under the surface, the item itself is not replaceable, if drilling into the surface will destroy the item, or if only a quick test is needed. In such cases, a surface-mounted microphone such as the Ultra-Thin Precision (UTP) microphone with an ultra-small form factor (only 1 mm profile) is ideal.