-
KEMAR >
-
-
-
-
-
-
-
R&D
-
PE
-
PL, QA and QC
-
-
-
-
Got a question?
If you have a question, feel free to contact us:
GRAS Sound & Vibration
Headquarter | gras@grasacoustics.com
UK | sales-uk@grasacoustics.com
USA | sales-usa@grasacoustics.com
China | cnsales@grasacoustics.com
GRAS worldwide
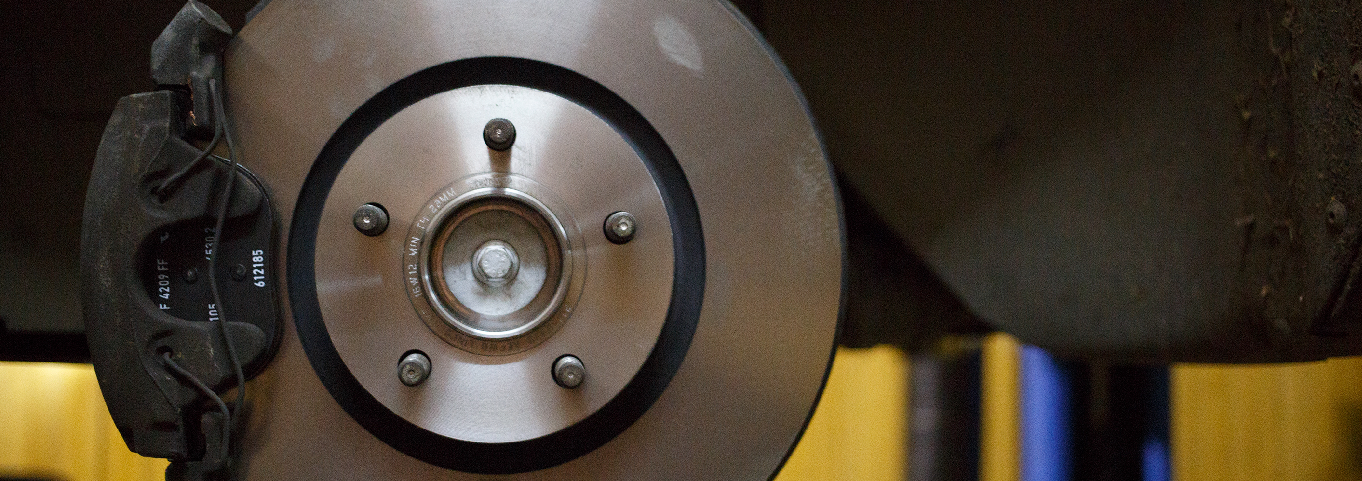
Brake Noise Testing
Brake noise is a chassis-related noise and a big problem for car manufacturers. The noise is caused by friction-induced vibrations, which make the brake system radiate noise. This will in turn cause a lot of irritation and disturbance to the car owner and any person near the vehicle when it occurs. The brake noise can lead to poor results in surveys of customer satisfaction and high warranty costs. Therefore, the development of brake systems with minimum noise issues are highly prioritized in the automotive industry. Brake noise is a very complex problem and the research in this area is in continuous progress.
On top of that, the electrification of vehicles requires new brake design as well as increased focus on noise since the auditory masking from the engine disappears. However, the traditional brake systems will be used to a lesser extent in an electric vehicle. There is a regeneration process during deceleration used to provide battery charging which in many cases will be sufficient to control the vehicle speed without using the brake pedal.
Read about electric application here.
The usual development process to avoid brake noise is divided into several steps that start when the requirements for brake performance have been defined:
-
Concept selection
-
Design review, best practice checks
-
Computer-aided engineering (CAE) noise predictions
-
Component testing, modal analysis
- Verification of modes for all brake components, especially pads and rotor
- CAE correlation -
System test, brake squeal
-
Vehicle test (started after approval of the system test)
The brake dynamometer squeal test and the wheelhouse test include testing with microphones. The noise characteristics from the most common brake type, i.e. the disc brake, are the following:
-
Low frequency (often broadband) noise between 100 – 1,000 Hz, referred to as scraping, grinding, grunt, groan, moan or judder depending on character.
-
Medium to high-frequency tonal noise between 1 – 5 kHz. This is a friction-induced noise typically caused by coupled modes between pads and rotor causing out-of-plane vibrations. The squeal starts at specific conditions of brake pressure, rotor temperature and environment.
-
High-frequency tonal noise, brake squeal or sometimes referred to as squeak above 5 kHz. This is also a friction-induced noise, but with exciting in-plane resonances of the brake rotor.
Learn more about the challenges and how to select the right microphone
Resources
Selected products
-
GRAS 147EB
A rugged microphone with extra protection for on-road testing in all climate zones and weather conditions -
GRAS 146AE
The perfect choice for test bench testing -
GRAS 42AG
The ideal solution for calibration
Brake Noise Testing on Electric Vehicles
As most EVs/HEVs are heavier than traditional ICE vehicles, the brake system is designed for braking higher mass. At the same time, there is increased focus on noise from the brakes since the auditory masking from the engine disappears.
However, the traditional brake systems are used to a lesser extent in an electric vehicle due to a regeneration process, taking place during deceleration by which the batteries are charged. In many cases, this will be sufficient to control the vehicle speed without using the brake pedal. Therefore, on-road acoustic brake testing is required.
For brake dynamometer testing, we recommend GRAS 146AE ½” CCP Free-field Microphone Set.
For on-road testing, we recommend GRAS 147EB CCP X-Rugged Microphone Set.
Please refer to SAE J2521 for detailed information related to brake noise testing.
See our complete application offering within electric vehicles here.
ACOUSTIC TEST TYPES WITHIN BRAKE NOISE TESTING
Brake dynamometer squeal noise test
Brake dynamometer squeal noise test is well defined and proved to make sure that the brakes will be in the best possible state when it comes to brake squeal before starting the vehicle testing. It is performed in a noise, vibration and harshness (NVH) brake dynamometer according to SAE J2521. Brake squeal is defined to be between 1 - 17 kHz. The brake dynamometer squeal noise test is done as per the following procedure:
-
The complete brake system is mounted in a fixture containing a vehicle corner, i.e. ¼ of the full chassis with suspension.
-
Several thousands of brake conditions are tested, among others at different wheel speed, brake pressure, rotor temperature, various environmental conditions and brake wear to mention a few.
-
A measurement microphone records the brake squeal.
-
Accelerometers register vibrations for correlation to the noise.
-
3D laser vibrometer or acoustic cameras are sometimes used for root cause investigations.
-
In the case of brake squeal noise exceeding acceptable levels, this test can be used for testing a range of different brake components. This includes modifications of the brake pads, the lining material composition, pad design, adding shims, mass loading and damping or modification of the rotor or caliper, including mass loading of the caliper.
Wheelhouse test
The final important testing is the road test. This is done at precisely defined test locations and test conditions for long periods to capture all, important driving, environmental and brake conditions. The noise is recorded inside the vehicle and in the wheelhouse simultaneously with numerous other parameters like brake vibrations, brake pressure, brake temperature, driving conditions, deceleration and, finally, the important subjective impressions.
The test needs to be repeated for many vehicles and for long mileages at all seasons, especially during wintertime. An OEM would for example use 25 cars equipped with four microphones in the wheelhouse, a reference microphone at the driver’s ear, and at least four accelerometers for driving the dedicated test cycles for 50,000 km (30,000 miles). Besides testing on different road conditions, this also includes other tests such as soaking in cooling facilities, driving on splash tracks before braking and other special tests. This allows the NVH engineer to capture brake noise results across all possible external conditions.