Got a question?
If you have a question, feel free to contact us:
GRAS Sound & Vibration
Headquarter | gras@grasacoustics.com
UK | sales-uk@grasacoustics.com
USA | sales-usa@grasacoustics.com
China | cnsales@grasacoustics.com
GRAS worldwide
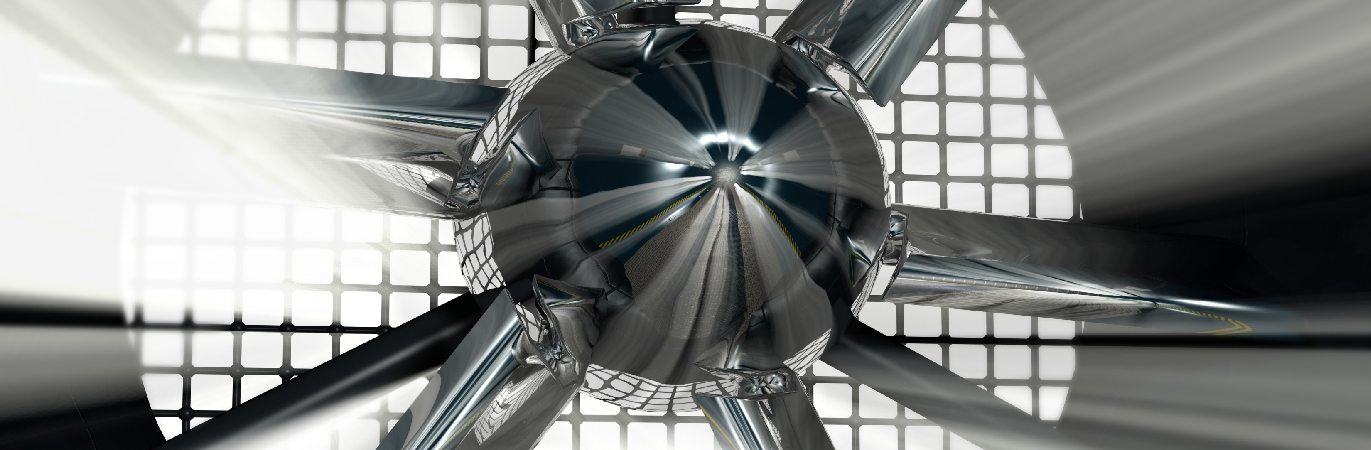
Aeroacoustics & Aviation Wind Tunnel Testing
The aviation industry is continuously aiming at increasing performance and at the same time reduce environmental noise emission and pollutant.
Understanding the aeroacoustics of an airplane or any other flying vehicle includes exploring aerodynamic noise, i.e. turbulent fluid motion and acoustic pressure fluctuations, i.e. external noise generation via aerodynamic forces interacting with surfaces.
Although in flight measurements are important, many tests and simulations are performed in wind tunnels. Main types of wind tunnels for aerospace and defense cover subsonic, transonic, supersonic and hypersonic wind tunnels – a main differentiator being the speeds in the test sections.
Jet and engine noises are obviously important fields of investigation that are tested in wind tunnels. Furthermore, despite the industry’s ongoing efforts to reduce noise, airframe noise generated by landing gear, flaps, slats or other high-lift devices are also still significant contributors to aircraft acoustic emissions. Other important tests include acoustic fatigue and shock wave noise investigation - important parameters that can be scale tested in wind tunnels.
This makes wind tunnel testing and noise path analysis under steady-flow conditions a very important component for minimizing vibrations and noise throughout aerospace vehicle design, certification and operation.
However, wind tunnel testing typically involves high costs linked to the preparation of the test item and operation of the wind tunnel and must be performed efficiently to get the most out of the limited testing time.
Mounting, demounting, remounting as well as verification of sensors become highly critical for ensuring reliable data easily, efficiently and within budgets.
Due to the complexity of measuring boundary layer sound pressure, it is still very difficult to simulate aeroacoustics and often requires multiple validation and correctional phases. Increasing computational power combined with precision microphones from GRAS – allows wind tunnel testing that help investigate new aircraft concepts, verify performance of innovative designs through experimental validations of CFD models, and validate prediction models long before the aircraft can actually fly.
GRAS provides a number of microphone solutions for testing scale models in wind tunnels as well as for in flight testing.
Discover the new Ultra-Thin Precision (UTP) microphones with an ultra-small form factor, only 1 mm in height.
Download our Measurement Microphone brochure.
Download our Turbulence and Measuring of Boundary Layers white paper.
Solutions
Due to the stochastic behavior of turbulence and flow-induced noise – also referred to as boundary layer noise – it is very difficult to quantify and understand these phenomena. In the development and testing stages of the aerospace, automotive and renewables industries. It has, therefore, been a key focus area for years – but has been hampered by a number of facts.
First of all, experimental tests have proven imprecise due to traditional microphone profile heights. Secondly, the mounting, demounting and remounting of sensors has been a tedious and not very user-friendly process. Finally, simulations and tests in anechoic wind tunnels are costly and most often require careful planning and coordination, making it very time-consuming.
GRAS measurement microphones for boundary layer applications cover UTP microphones, surface microphones and flush-mount microphones – available for surface mounting, “blind window” mounting, destructive mounting or wire-mesh applications.
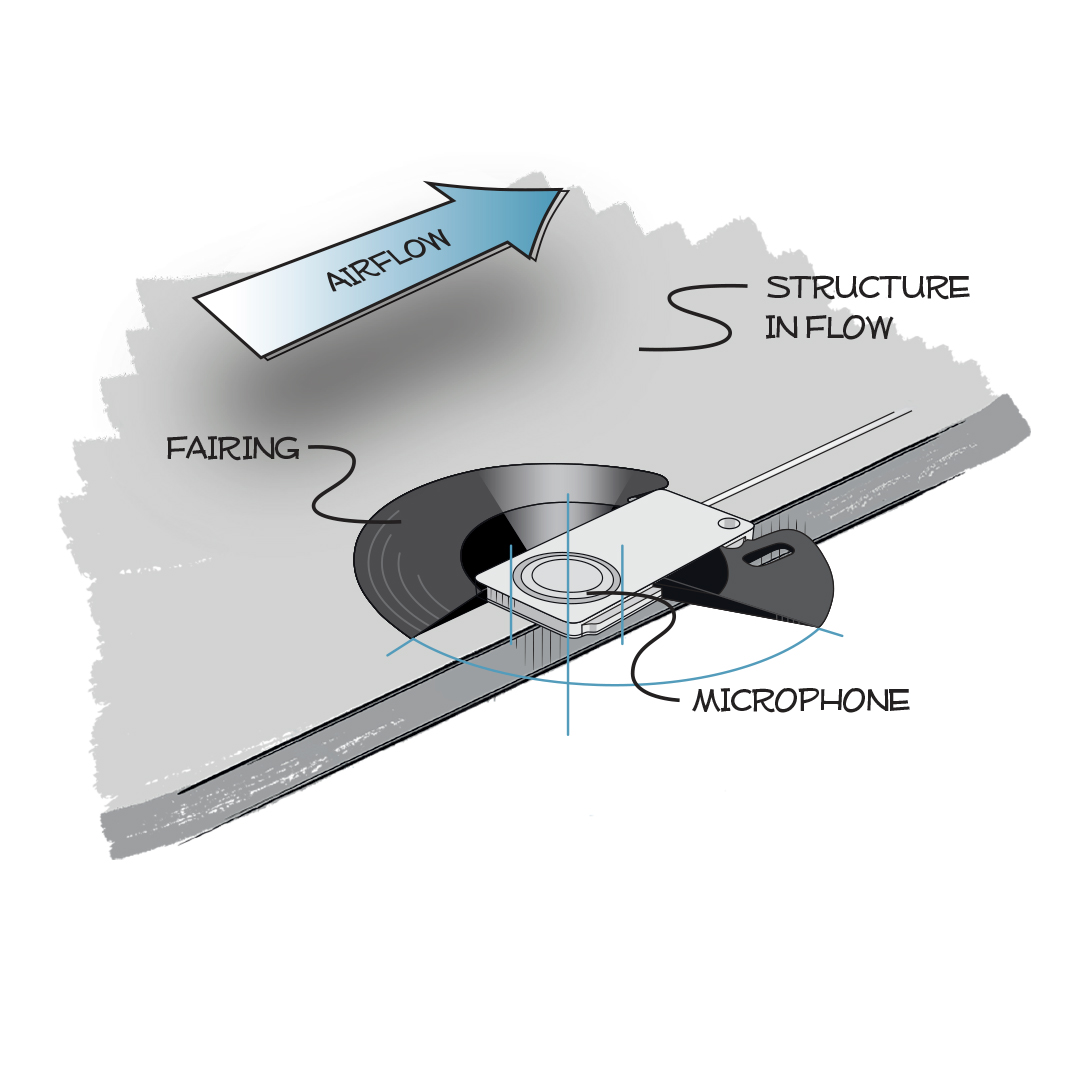
Schematic of UTP microphone, 48LA/LX-1.
UTP Microphones – Ultra-Thin Precision Microphones
The GRAS UTP microphones combine the high precision and reliability of GRAS measurement microphones with the need for extremely low-profiled (less than 1 mm) microphones with minimum turbulence influence. With their unique form factor and easy mounting, UTP microphones are specifically designed for in-situ boundary layer testing, when neutral impact and high precision is important. They combine the accuracy of condenser microphones with an extremely small form factor. All LX versions have TEDS.
> High-precision measurement microphones
> Ideal for low-boundary layer testing and confined spaces
> Fast and repeatable mounting with consistent geometry
> Easy in-situ verification
> Wide linear frequency range
> Wide dynamic range
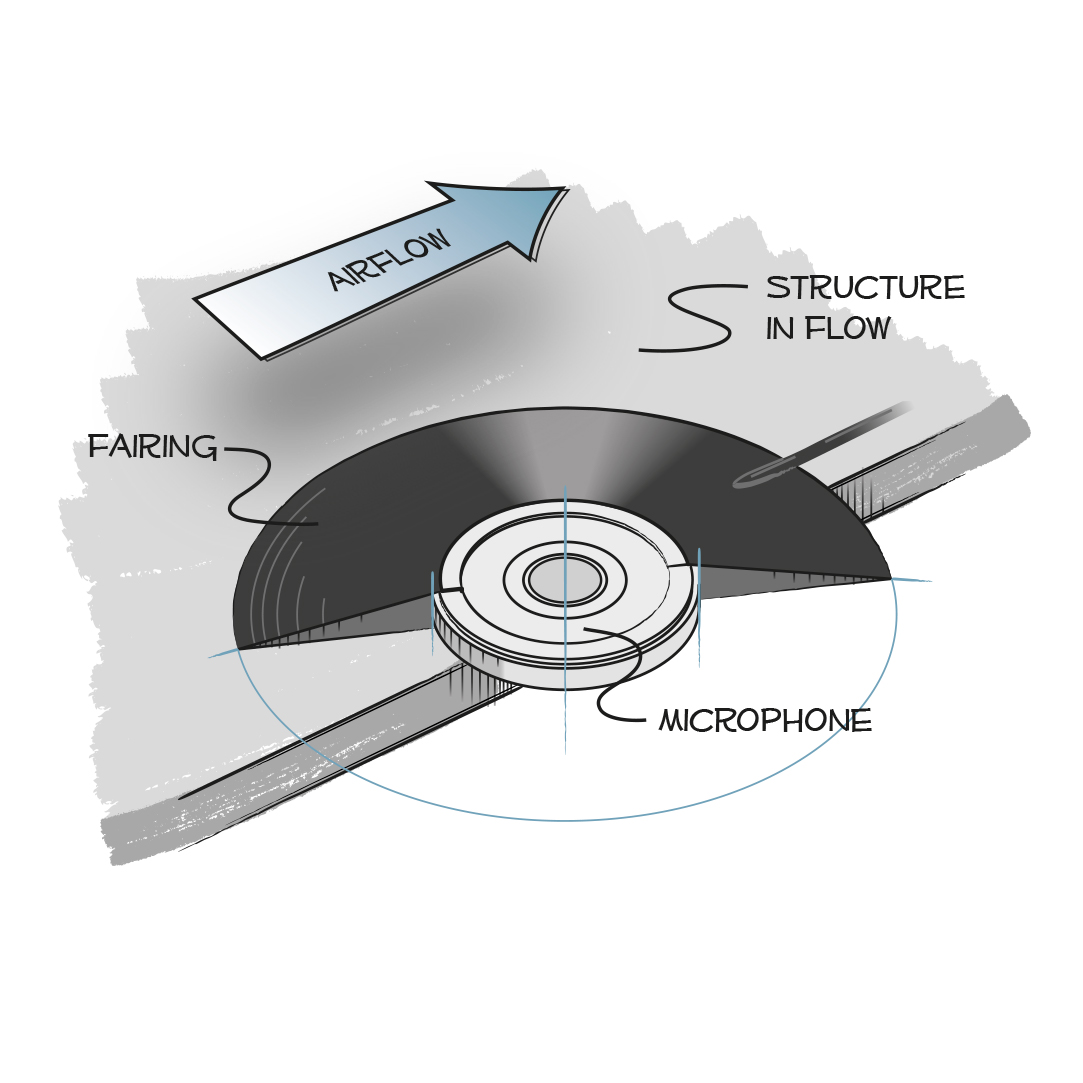
Schematic of surface microphone, 40LS.
Surface Microphones
The GRAS high-precision surface microphones are designed for in-situ boundary layer testing, where non-invasive mounting is necessary.
They are therefore also well suited for in-flow testing of full-scale objects in wind tunnels.
The height has been kept at 2.5 mm, and a fairing reduces self-generated turbulence.
> High-precision measurement microphones
> Non-invasive mounting and insignificant protrusion
> Integrated preamplifier with plug and measure functionality (TEDS)
> Wide linear frequency range
> Wide dynamic range
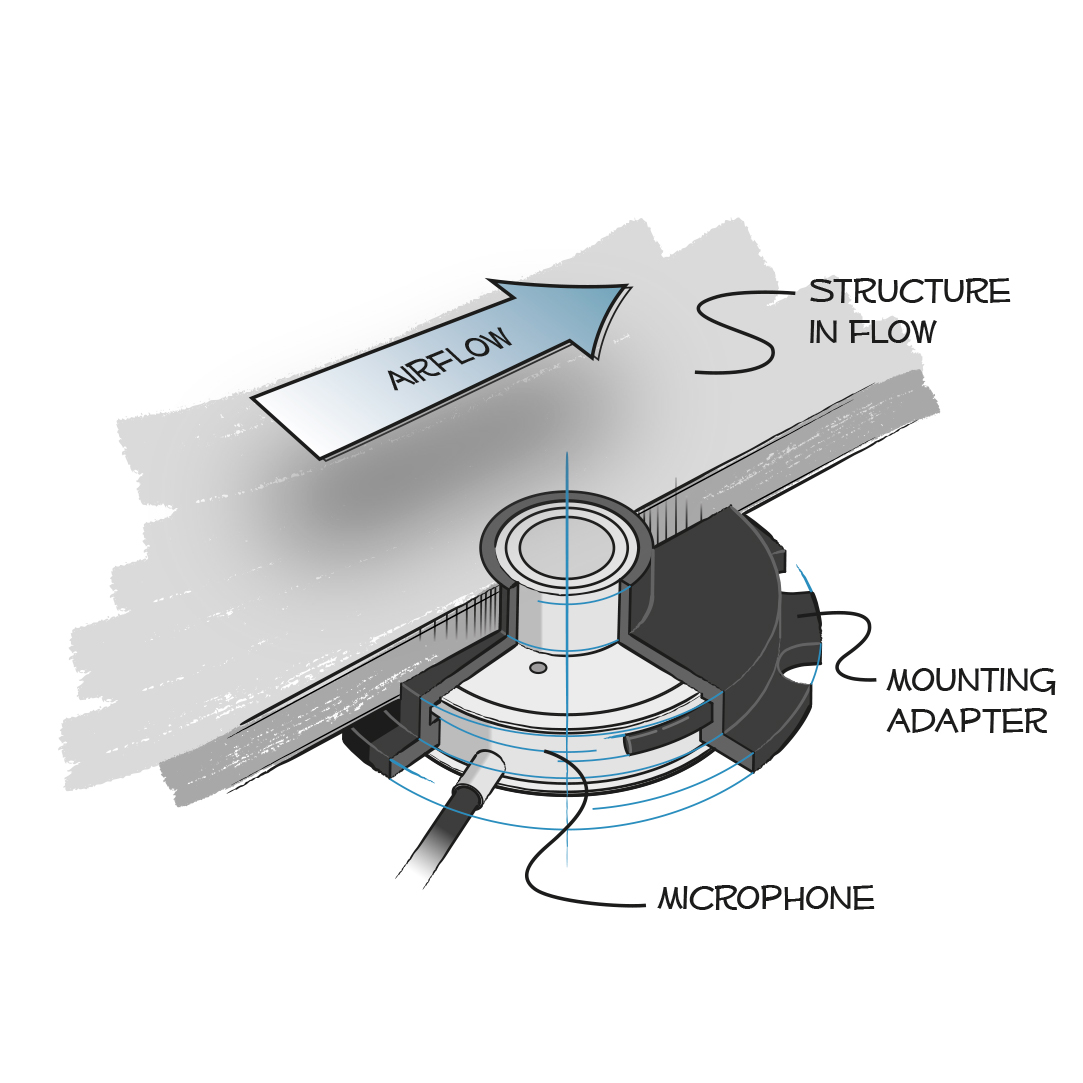
Schematic of flush-mount microphone, 47BX.
Flush-mount Microphones
This line of acoustic sensors combines the high precision and reliability of GRAS measurement microphones with the need for fitting sensors into very confined spaces and narrow structures.
With an installation height of less than 10 mm, GRAS flush-mount microphones can be integrated into virtually any design without sacrificing aerodynamic properties.
> High-precision measurement microphones
> Very low installation height
> Integrated preamplifier with plug and measure functionality (TEDS)
> Wide linear frequency range
> Wide dynamic range